آهن اسفنجی به طور مسقیم از احیای سنگ آهن طبیعی (Direct Reduced Iron) بدست میآید و از مواد اولیه ساخت فولاد است. 5 درصد از فولاد جهان با استفاده از آهن اسفنجی ساخته میشود.ایران و هند بزرگترین تولیدکنندگان آهن اسفنجی در جهان می باشند.
آهن اسفنجی منبعی با عیار بالا برای ساخت آهن و فولاد است که از سنگ آهن طبیعی پیش از رسیدن به دمای ذوب به دست میآید و از مواد اولیه برای ساخت آهن و فولاد است که عیار بالایی نیز دارد. برای ساخت آهن اسفنجی، گندله سنگ آهن (عیار ۶۷% ) را احیا و آهن اسفنجی (گندله متخلخل) با متالیزاسیون fe ( حدود ۹۲ درجه) به دست میآورند.

ساختار آهن اسفنجی
آهن اسفنجی، از لحاظ ظاهری قطعاتی کروی شکل (گندله) است که به دلیل متخلخل بودن ساختار اسفنجی پیدا کردهاست. عیار بالای این ماده، کم بودن آسیبهای زیست محیطی آهن اسفنجی نسبت به مواد دیگر، باعث شده تا آهن اسفنجی برای تولید فولاد بسیار مورد توجه قرار گیرد.
فرآیند تولید آهن اسفنجی با استفاده از منابع گازی و زغال سنگ
تولید آهن اسفنجی از سنگآهن، عموماً به دو روش گازی (Gas Based) یا استفاده از زغالسنگ (Coal Based)، برای احیای آهن صورت میپذیرد. معمولاً در کشورهایی که دارای ذخایر گاز هستند، از روش گازی استفاده میگردد. در ایران نیز بهطور مثال، فولاد خوزستان و فولاد مبارکه از گاز به عنوان ماده احیاکننده استفاده میکنند.
روشهای ساخت آهن اسفنجی با استفاده از گاز طبیعی شامل موارد زیر هستند:
روش H.Y.L اچ وال ال
روشPurofer پروفر
روش Midrex میدرکس
تولید آهن با استفاده از زغال حرارتی
تولید آهن اسفنجی با استفاده از زغال حرارتی به روشهای زیر انجام میپذیرد.
فناوریهای تولید آهن اسفنجی مبتنی بر روش (RHF) Rotary Heart Furnace
تولید آهن به روش ITmK3
فنآوری تولید آهن اسفنجی در کوره دوار به روش SL/RN
فرآیند Corex
تولید آهن اسفنجی به روش میدرکس
روش میدرکس، یک تکنولوژی آمریکایی و رایجترین روش مورد استفاده در ایران، است، چرا که کم مصرفترین و پربازدهترین روش است. (حدود 80 درصد آهن اسفنجی در ایران از این روش تولید میشود). در این روش با ورود گاز طبیعی به واحد شکست گاز، با کمک حرارت و کاتالیستهای خاص، به هیدروژن و کربن شکسته میشود. پس از آن، هیدروژن و کربن را وارد کوره احیا که گندله سنگ آهن در آن گداخته شده است، کرده تا با اکسیژن گندله ترکیب و سنگ آهن را احیا کند.
کاربردهای آهن اسفنجی
از کاربردهای آهن اسفنجی میتوان به استفاده از آن بهجای ضایعات آهن در فرایند ذوب اشاره کرد. کاربردهای آهن اسفنجی در کورههای القائی بسیار بیشتر از دیگر روشهای ذوب است؛ زیرا در این روش میتوان با داشتن تجربه و دانش کافی، نزدیک به ۵۰ درصد آهن اسفنجی را جایگزین آهنقراضه کرد. همچنین از دیگر کاربردهای آهن اسفنجی میتوان به ساخت آهن فرفورژه یا فولاد فراوریشده اشاره نمود.
با افزایش دانش و بهبود روشهای ذوب، امروزه مشکلات به کارگیری آهن اسفنجی بهجای ضایعات آهن به حداقل رسیده و از این محصول در بسیاری از واحدهای کوچک و بزرگ فولادسازی استفاده میگردد. «بریکت» یکی از فراوردههای حاصل از آهن اسفنجی است.
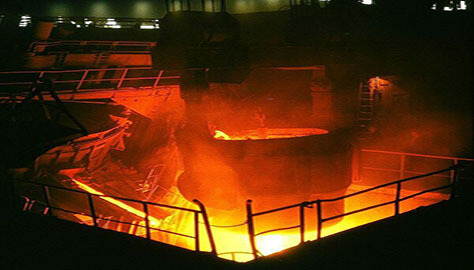
مزایای آهن اسفنجی نسبت به قراضه
کیفیت فلزکاری بالا
گوگرد و فسفر کمتر
حاوی عناصر زائد کمتر نسبت به قراضه آهن
روش سریعتر از قراضه آهن
روش احیای مستقیم از روش کوره بلند ارزانتر است.
روش احیای مستقیم نسبت به روش کوره بلند دارای محدودیتهای زیستمحیطی کمتری است.
عیار بالاتر نسبت به آهن خام
استفاده از روش احیای مستقیم در واحدهای کوچک فولادسازی نیز توجیه اقتصادی دارد.
سهولت حمل و ذخیره آهن اسفنجی بهصورت آهن گرم کلوخه شده (HBI)
امکان استفاده از گاز طبیعی بدون حذف ناخالصیهای آن درروش احیای مستقیم وجود دارد.
چگالی آهن اسفنجی
چگالی آهن اسفنجی نسبت به آهنقراضه بیشتر بوده و بنابراین میتوان مقدار کمتری آهنقراضه به کوره شارژ کرد. چگالی آهن اسفنجی در شکل کلوخه 1.80 gm/cc و در شکل نرمه 1.75 gm/cc بوده و میزان عیار آن بین ۸۴ تا ۹۵ درصد است.
خطرات آهن اسفنجی
قابلیت اکسیداسیون و زنگزدگی از خطرات آهن اسفنجی است؛ بنابراین باید حفاظی برای آن در نظر گرفته شود و در صورت امکان در اسرع وقت به فولاد تبدیل شوند. همچنین از دیگر خطرات آهن اسفنجی میتوان به امکان اشتعال آن در حالت خمیری اشاره نمود.
برای جلوگیری از اکسیداسیون آهن اسفنجی میتوان توسط گاز خنثی، سیلیکات سدیم، آهک و سپس قرار دادن در فضای سرپوشیده و بریکت سازی از این محصول حفاظت نمود.
تفاوت آهن اسفنجی و گندله
گندله سنگ آهن از کنسانتره سنگ آهن به دست می آید. کنسانتره آهن، سنگ آهن آسیاب شده است که به دلیل سایز بسیار ریز قابلیت استفاده در واحد های ذوب و حتی واحد های احیاء مستقیم را ندارید. به همین دلیل کنسانتره آهن بعد از فرآوری، تبدیل به گندله می شود. گندله آهن به دست آمده هم می تواند در واحد های ذوب مورد استفاده قرار بگیرد و هم در واحد های احیاء مستقیم.
روش تولید گندله
برای ساخت گندله مواد اولیه که شامل کنسانتره و سنگ آهن خرد شده با ابعاد کمتر از صد میکرون است را به همراه برخی مواد دیگر مانند بنتونیت، آهک، آب و ... در داخل دستگاه های مخصوص تولید گندله که می تواند به صورت استوانه ای یا دیسکی باشد وارد می کنند. در اثر حرکت دورانی هر کدام از این دستگاه ها، ذرات سنگ آهن به همراه مواد افزودنی که نقش چسب را ایفا می کنند به هم متصل می شوند و تشکیل یک گلوله را می دهد. از طریق برخی از تنظیمات بر روی دستگاه تولید گندله می توان ابعاد گندله را تنظیم کرد. گندله هایی که از دستگاه گندله سازی خارج می شوند به دلیل اینکه از استحکام کافی برخوردار نیستند نمی توانند در کوره بلند و یا برای حمل ونقل استفاده شوند. به همین دلیل طی فرایندهایی مانند خشک کردن، پیش گرم کردن، پختن و سرد کردن گندله های تولید شده می توانند برای مصرف احیای مستقیم یا کوره بلند مورد استفاده واقع شوند.
نرمه آهن اسفنجی (DRI Fine)
پس از سرند، نرمه آهن اسفنجی که محصول آهن اسفنجی با ابعاد کمتر از 6 میلیمتر است، جدا شده و در صنایع مختلف مانند تولید لنت خودرو استفاده میشود.
بریکت (Briquette)
برای انبار و ذخیره راحتتر آهن اسفنجی (DRI)، آن را غلیظ و فشرده میکنند و به آن بریکت (Briquette) میگویند. ساخت بریکت از این جهت که منجر به کاهش تخلخل (جداسازی) سطح و افزایش دانسیته و مقاومت در برابر سایش است، یکی از بهترین روشها برای کاهش اکسیداسیون یاهمان زنگ زدگی آهن اسنفجی است.
بریکت گرم
بریکت گرم در درمای بالا ( بیش از 650 درجه سانتیگراد) از آهن اسفنجی گرم (HBI)ساخته شده و پرکاربردترین بریکت است.
بریکت نرمه و برکیت سرد آهنی
برای ساخت دو محصول بریکت نرمه و بریکت سرد، مواد را در دمای محیط وارد ماشین بریکت زنی میکنند، فرآیند بریکت سازی سرد، تکنولوژی جدیدی است که باعث توسعه و آسانی حمل و نقل و ذخیره آهن اسفنجی برای تولید فولاد در واحدهای احیای مستقیم شدهاست.
کاربرد بریکت
آهن و فولاد
مواد معدنی (دولومیت، منگنز، فروآلیاژ، آلومینا، آهک)
مواد شیمیایی (سولفات ها، کربنات ها، کلریدها، سیانیدها، برومیدها)
کودهای شیمیایی
مواد شوینده و بهداشتی
لجن آهن اسفنجی (DRI Sludge)
پس از تهیه آهن اسفنجی، ریزدانههای آهن اسفنجی پس از برخورد با گازهای احیایی شسته شده و به حوضچههای جمعآوری ذرات انتقال و رسوب میکنند. این ریزدانهها را در فضای انبار آب تخلیه میکنند و سپس این مواد همراه با آب تبخیر، برای مخلوط با سایر بارهای فلزی برای تولید گندله و یا آگلومره کاربرد دارند.
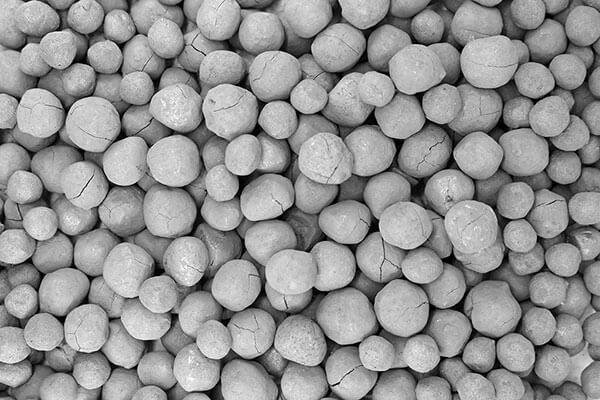
اطلاعات آنالیز آهن اسفنجی و برگه اطلاعات ایمنی محصول را میتوانید از طریق لینکهای زیر دانلود نمایید.
دانلود آنالیز آهن اسفنجی
دانلود برگه اطلاعات ایمنی آهن اسفنجی